In May 19, 2017, Nanjing Allied Rongda Engineering Material Co. Ltd. successful completed the hearth crucible casting project on 1#450 blast furnace of Ulanhot iron and Steel Co. The project includes casting of the whole ceramic cup and tuyere zone. A total of 265 tons of special castable refractory were installed for the project. And the project finished 36 hours in advance compared to planned time, because of excellent organization. The Allied Rongda team is ready to carry out the installation of the whole iron runner of the blast furnace, from zero.
Monolithic casted hearth crucible of BF is an Allied Rongda’ self-developed technology. The principle of the technology is that a monolithic casted ceramic cup on the residual carbon brick hearth is a perfect prevention of dissolution of carbon brick being dissolved by liquid iron and heat transfer. It is considered an effective method for safe production and prolong the service life of the blast furnace at the later service period.
The technology is applied on a re-build BF for this project at Ulanhot Iron and Steel Co.. A monolithic ceramic cup is casted on a newly installed brick hearth.
After a generation of campaign for 8 years, all the residual hearth refractory of the 1# 450BF were removed. All the carbon bricks in the hearth were re-built, and a new monolithic ceramic cup were casted on the new carbon brick hearth. According to the practical situation of the project, Allied Rongda team of technical experts designed the maintenance plan, formulated the engineering schedule. The installation project was then completed by our professional installation team, in accordance with the time schedule, under the all-time supervision, with serious control of the detail by our technical experts.
The well organization and high quality and 36 hours earlier completion of the project won high praise by the officers of the iron plant. More cooperation on other refractory installation projects are on discussion.
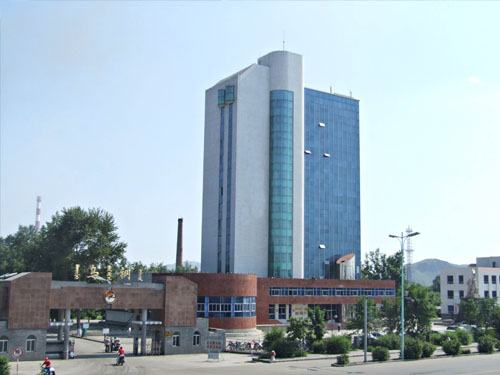
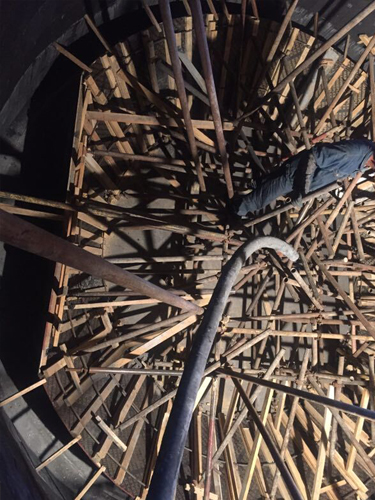
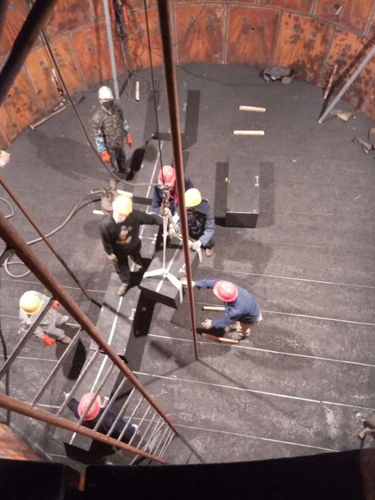
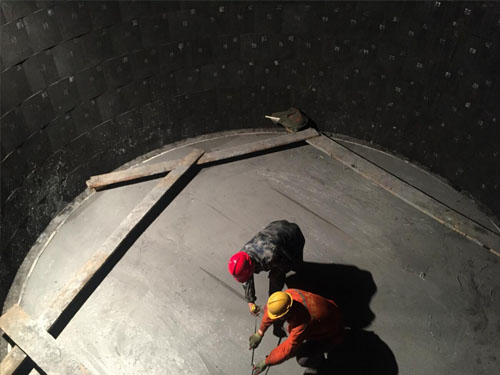
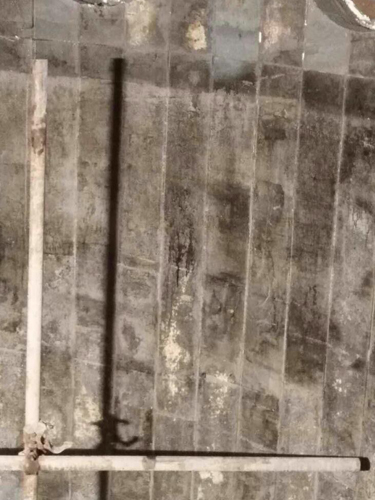
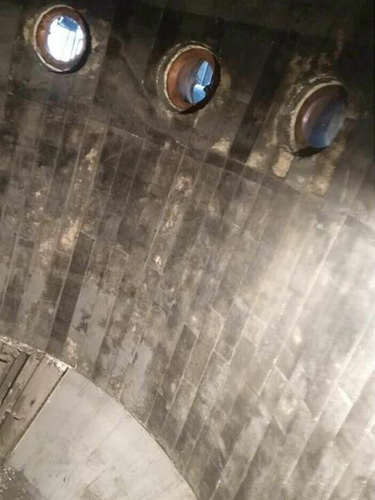
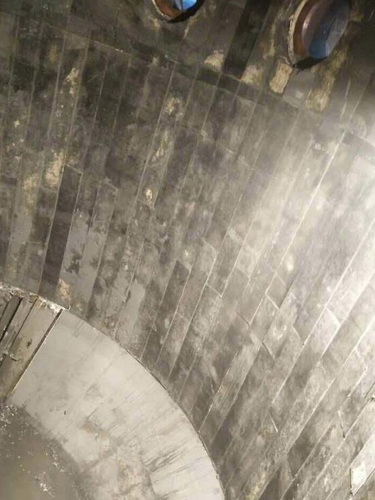
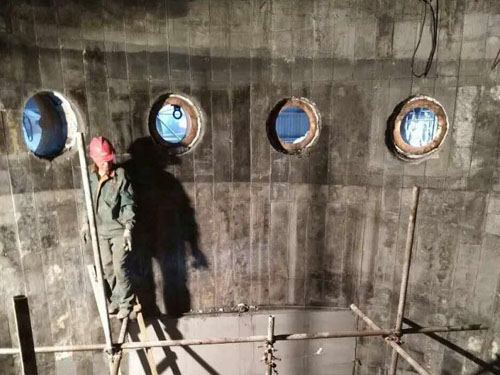