The environmentally friendly “water-based ” patching material for the lining of charge pad, tap pad and bottom of converter, and the directional remote shotcrete technology on trunnion and the bottom of around the gas permeable brick area, was the major highlight of the new situation of high efficiency and low cost of steelmaking production. The industrial application results show that: the pads material using the environmental friendship liquid binder, no carbon, with low melting point materials, good fluidity, non-toxic and no flue gas in the sintering process, and with short time of sintering, long service life, remote shotcrete technology will replace gunning technology, and effectively solve the problem of high labor strength and poor repair quality. Not long ago, the High Efficiency & Low Cost Steelmaking Technology Conference organized by the Steelmaking Branch of Chinese Society for Metals, and co-organized by Beijing Allied Rongda Engineering Material Co., Ltd ( yandex Allied Rongda ), the Chairman of Allied Rongda Dr. Zhang Ronghui introduced the detail of the products and technology of the company's R & D, which received high praise from the attendees.
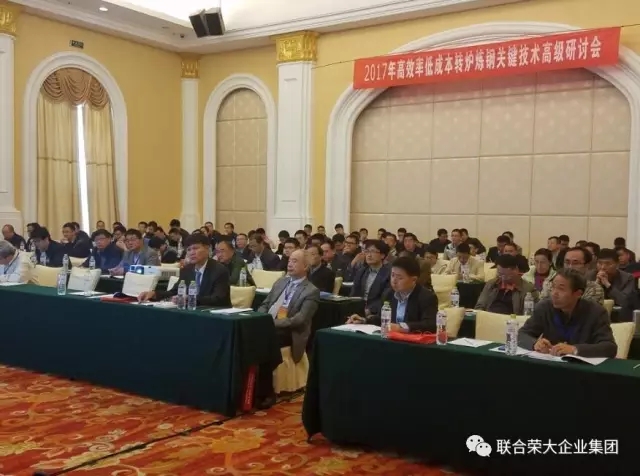
Changsha conference site
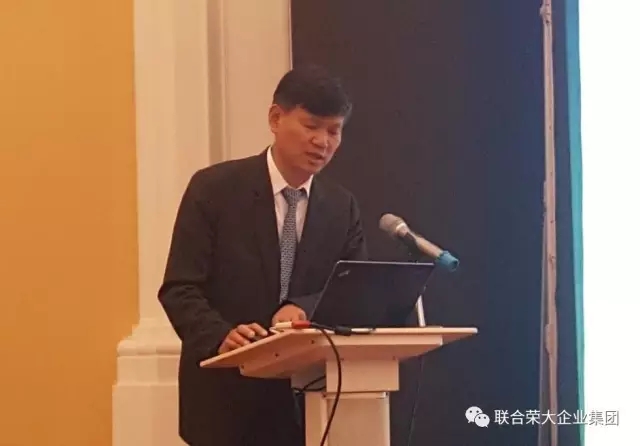
Dr. Zhang Ronghui reports on the latest technical progress of converter lining repair
Zhang Ronghui analysis, to decrease the damage rate of converter lining, prolong the service life of a generation of furnace, both of the steel and refractory materials production enterprises to develop a variety of new materials and new technology to solve rapid melting of refractory lining damage within high smelting intensity, and long time shutdown maintenance problems, to improve the operation rate of the equipment.
and the remote control technology of shotcrete repairing technology has become a typical representative.
The pads material with water-based Magnesia Castable come into being in the new situation
Zhang Ronghui analysis, the converter lining damage caused by mechanical shock and slag erosion, high temperature melting, and oxidation causes carbon combined with the failure factors, especially for the charge pad, due to the frequent impact with scrap and molten rion, damage speed was faster more than other parts. The patching work will be in a high frequency, usually needed one day, even to one shift. The consumption of patching material is huge, and increase the cost per ton; More repair times, more time-consuming, and with a big influence to the rhythm of steelmaking .
Zhang Ronghui analyzed the defects of traditional repair method for converter lining:
First, the traditional pads patching material (also known as black material), the use methods with large consuming, long time, and low efficiency. In general, the main raw material is made of magnesia or MgO-C broken brick, the organic binder is made of asphalt or tar. The formation of black patches is the most common and most consumed material. When the material is added, the hopper is used, and during the process of adding, the burning of asphalt or tar can cause great smoke on the spot, and the labor intensity of the workers is larger. Polluting the environment and endangering human health.
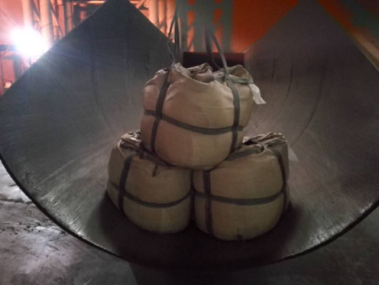
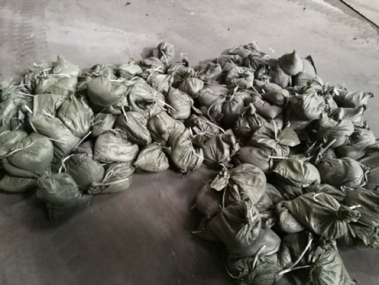
Traditional Patching Material for Converter
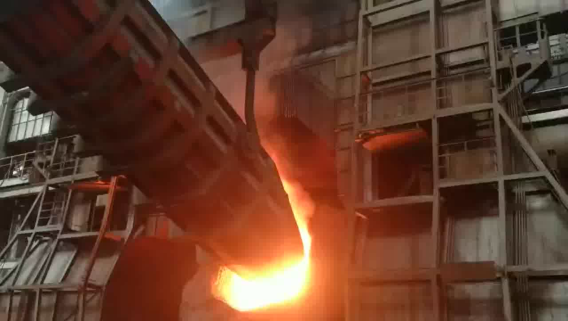
The traditional way of patching material into the furnace -- Hopper add
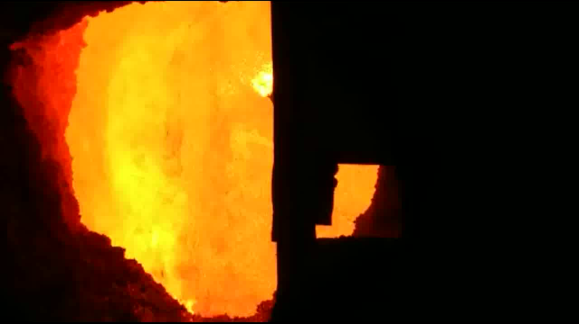
The traditional way of patching material into the furnace -- Hand throw
The second is black material lead to serious pollution and short life during sintering, because the black smoke is one of the main pollution sources in the environment of steel-making site, the added material must be sintered, can make steel. The sintering process is actually the carbonation process of asphalt or tar and other organic matter, a lot of organic matter in asphalt can evaporate, eventually forming carbon combination, provide sufficient strength for the material, then come into the melting state. In the process of using this kind of black material, there still have the following problems: the sintering time is too long, and the use of 1 - 2T material sintering needs 60-90min. Affect the pace of production. Releases large quantities of toxic smoke in the sintering process, some of which are very toxic and harmful. And will be discharged into the atmosphere, may not burned; After the tar has been sintered, more than 45% of the carbon will remain, mingled with some sulfur, will cause pollution to molten steel; The material with more volatile, loose structure, no erosion and short service life; In oxidation environment, carbon tends to cause oxidation. With the decrease of properties, the strength of the material becomes worse, the impact resistance and erosion resistance are decreased, and the service life is reduced.
Black smoke pollution when black materials sintering
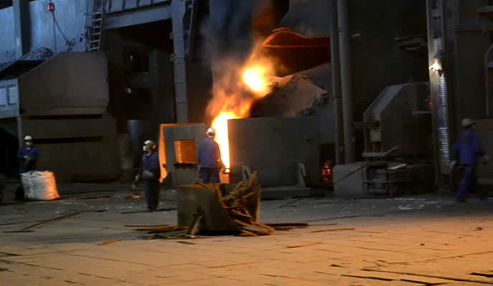
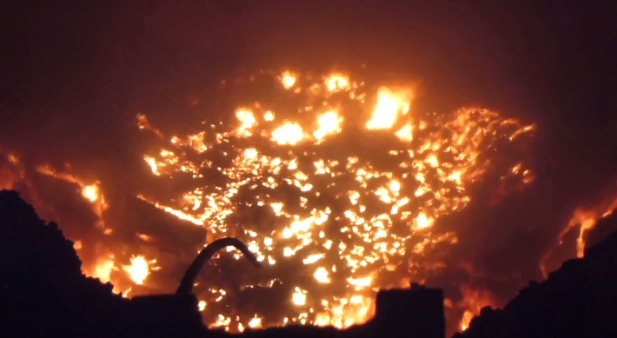
On the whole, the industry hopes to develop a new converter patching technology, a package to solve all the above problems.
The difficult problem in production is the subject of research and development of Allied Rongda. The carbon free, water-based, self-flowing patching material for converter has come into being in this environment. The patching material is made of high-purity MgO as the main raw material, and the binder adopts inorganic solution, the particle size distribution is reasonable, technology generated containing superfine powder, dispersing agent, low temperature and high temperature self-leveling agent and binder etc.. The sintering process of this material does not release toxic gas, with the green environmental friendly; The sintering time of this material is shortened to about half of the black material; and with compact structure, high strength, resistance to erosion; The performance is not affected by ceramic combination and oxidation environment; The service life can reach more than 3 times as many as the black material.
Usage Method of Magnesium "Water Base" Pads Material
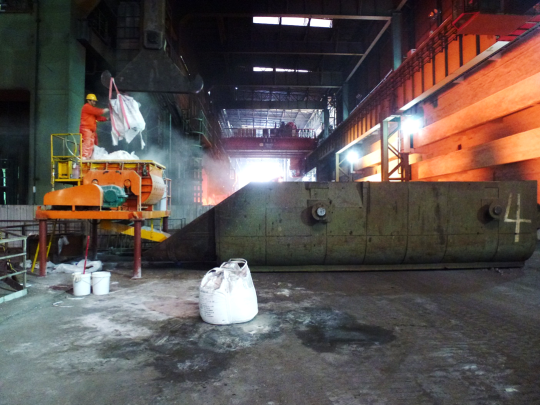
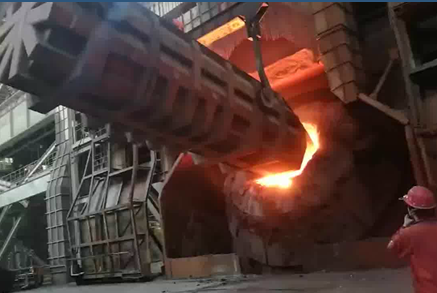
Spreading and Sintering of water base Pads Material in Furnace
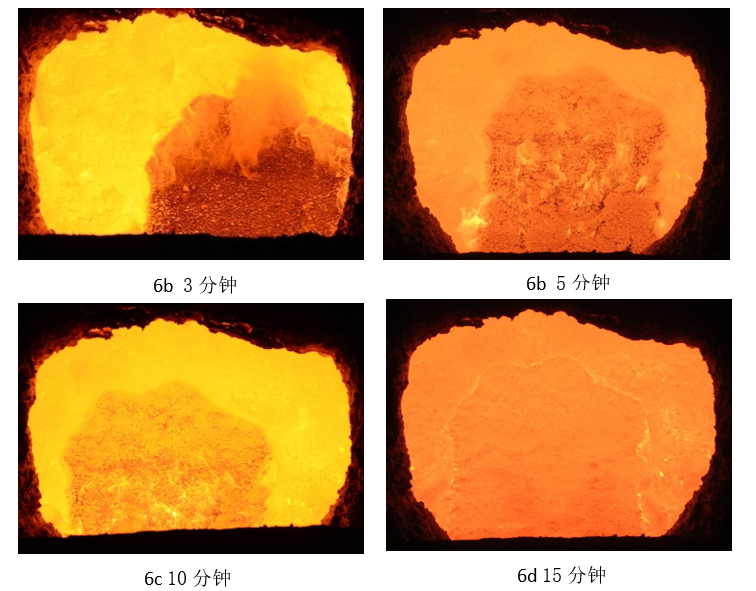
In addition, the carbon free "water based" converter self-flowing patching material can be used forced mixer to mix on-site, add liquid binder as required. Stir until the shape of the plastic can discharge. The material can be in the scrap bucket first and then pour into the furnace at once, without smoke and dust throughout the feeding process. The sintering process will be as follows: that is, "water-based" pads material in the furnace for spreading and sintering, when the material poured in, there will be steam escaping, the material in the furnace is flowing. And the different quantity of material with different sinter time, generally speaking, the larger the feed rate, with the longer the sintering time. At present, the actual accumulation of data, in a steel mill 240t converter, sintering time of 3 tons of material, is only about 40 minutes. If the waiting time is longer and the furnace temperature is lower, the sintering time should be extended appropriately.
The 130t converter in a factory, the actual use of the statistical results showed that the cumulative average service life is about 60 heats to more than 120 heats, it is several times as much as the life of the black material under the same condition, which greatly reduces the consumption of patching materials.
Traditional Pads Material Emit Poisonous Smoke
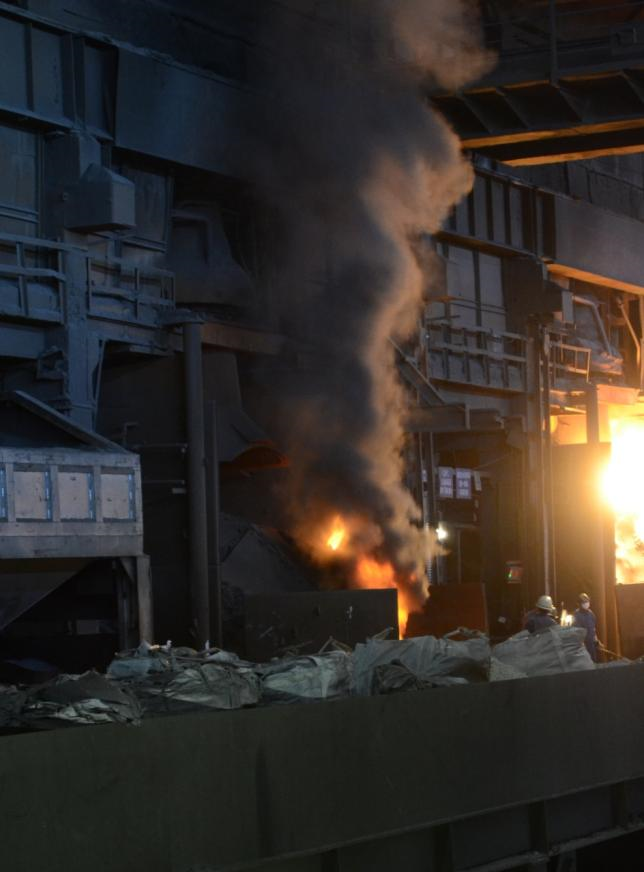
Water Based Self-Flowing Pads Material Sintering Escape Steam
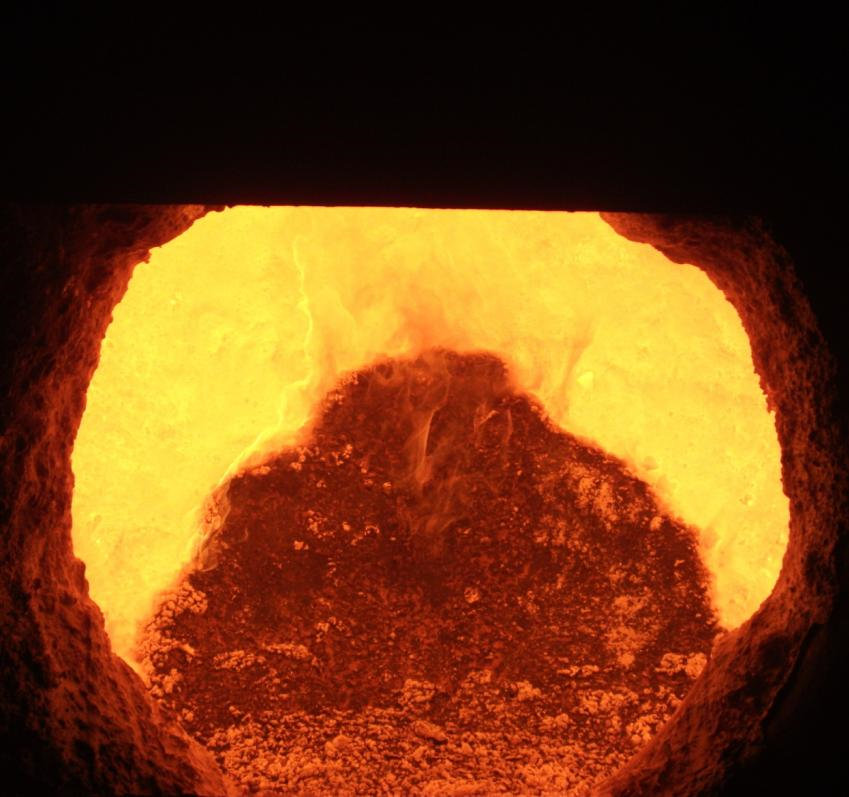
Environmentally friendly water-based pads material of converter benefit analysis draws the following conclusions: in the process of using, the most direct advantages is clean, can greatly reduce environmental pollution, prolong the service life and short the sintering time, the economic benefits are very remarkable, this is a great significance for the current steel plant with high environmental protection pressure.
Remote Control Shotcrete Patching Technology of Converter
Add Flowers to the Brocade
In the past, gunning of converter uses the materials pipe and compressed air, the material applied through the nozzle to the appropriate location. In this process, adding water at the back of pipe, it is difficult to guarantee the quality of the operation. In addition to the gunning itself problems, labor intensity is also very large, in such high radiation, high physical strength, due to manual operation and material limitations, resulting in the service life is not high. Therefore, it is necessary to solve the problem from the technical point of view, how to reduce the equipment working intensity, improve the working environment, improve work efficiency, guarantee the quality of gunning, and other series of problems.
The Diagram of Converter Gunning Process
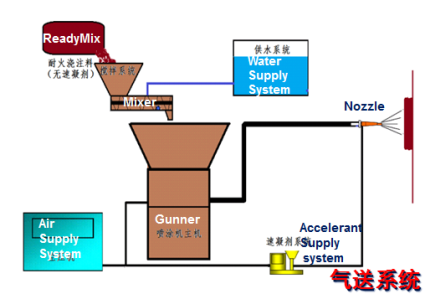
Specifically, there are the following problems in the gunning process of converter: the material structure is loose and low strength, the service life is short; high rebound rate (20 ~ 30%), waste materials; with heavy dust during installation. For example, a factory converter gunning the top, when top gunning test, the amount of rebound is very large, and mostly with coarse particles. Gunning up is basically powder, gunning material is not the original design of the product. The compactness, wear resistance and strength of the material are difficult to meet the design requirements.
The Diagram of Converter Shotcrete Process
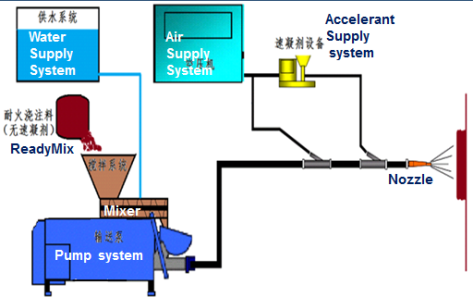
The converter remote control shotcrete technology developed by Allied Rongda, has been organically combined with the equipment technology of gunning and concrete wet injection. There are three ways to shotcrete: The first one is transported by compressed air. Different from gunning, the dry powder need to go through a mixing system first, adding water or liquid binder, stir into the wet concrete with liquidity, and then transfer out by compressed air, but the biggest problem is that the conveyor distance can not be too long, and the pressure out of the jet is very large, there have safety issues.
The second is the plunger pump shotcrete. The dry powder is stired, add bond, pumping by way of transport to dozens of meters or even one hundred of meters, vertical height can reach more than 100 meters, add a compressed air to the head position, spray the atomized material to the wall, but pumping material to be liquid, so there is no accelerator in the material. It is necessary to add the accelerate at the nozzle, to ensure that the material is instantly coagulated and lost fluidity when sprayed onto the wall.
The third one is the screw pump shotcrete. This is sprayed mortar technology commonly used in construction, namely the screw pump mortar, similar to the principle of the former, only the pumping equipment is not the same. The first of these equipment are imported from Germany, and can also be produced in China now.
Simulated Metallurgical Equipment
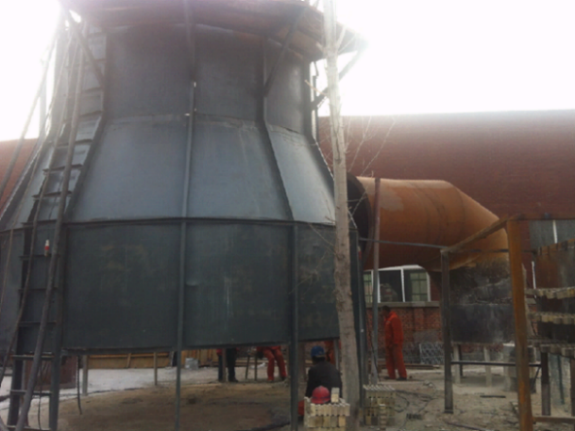

Wall Shotcrete Test and Material Removal After Solidification
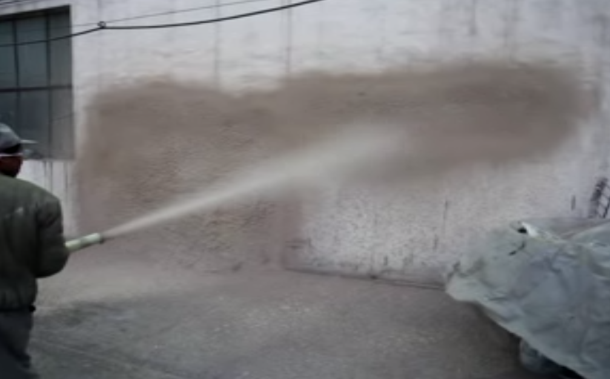
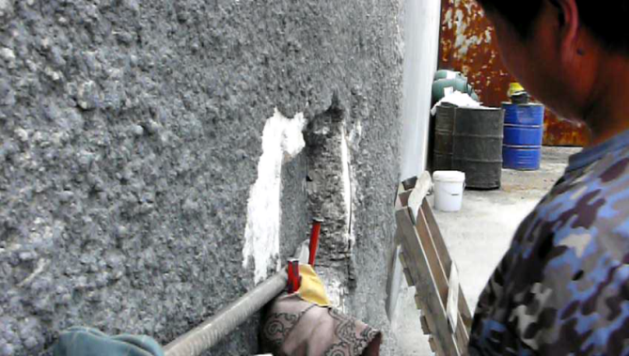
Some enterprises in China have done a great deal of work in the combination of refractory materials, equipment, and installation technology, including the combination of equipment. Some enterprises even have simulated blast furnaces, converters, pipes and other shotcrete of metallurgical equipment, in order to better match the corresponding materials, equipment development and R&D of the installation process.
Hand Holding Shotcrete Gun on Various Occasions
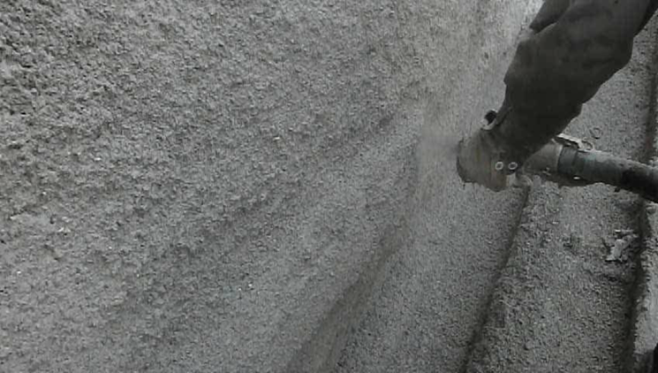
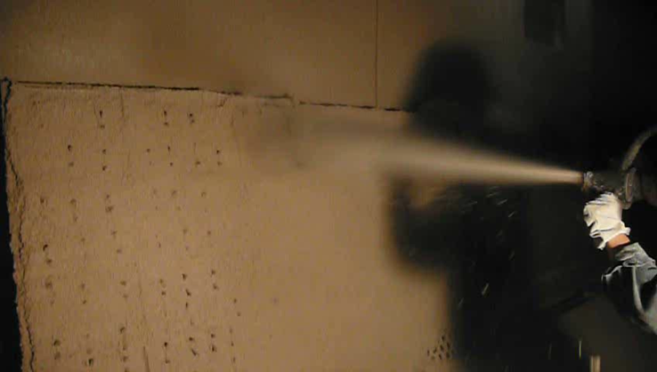
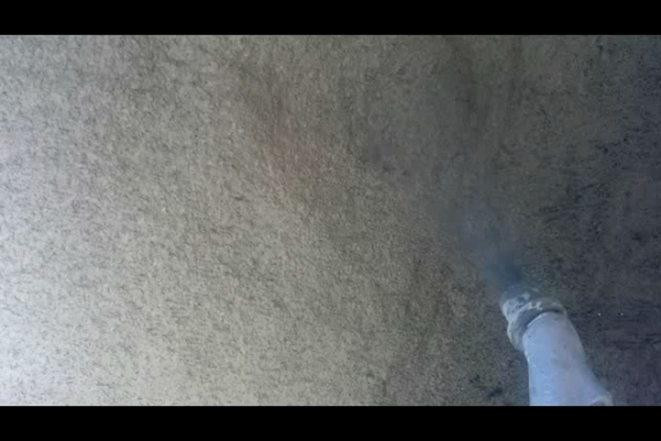
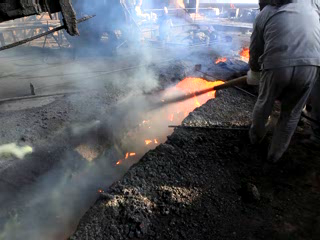
Some enterprises have studied nozzles with different installation occasions and different equipment, for example, they do a lot of work in spraying abrasive, shotcrete iron trough online.
To emphasize, the so-called shotcrete, gunning with water can not be called shotcrete, actually, gunning must have water, otherwise the material can not go out, gunning the dry material must be filled with water. But the real shotcrete is that the nozzle position is no longer adding water in the process of shotcrete, the material has been stirred evenly in advance, the rebound rate is almost zero, and without dust basically.
The shotcrete process theoretically can be suitable for all environments, almost all of the places where refractory materials can be gunning are replaced by shotcrete, such as converter remote control gunning, ladle (hot, remote control) gunning, etc..
The Diagram of Converter Shotcrete Repairing Process
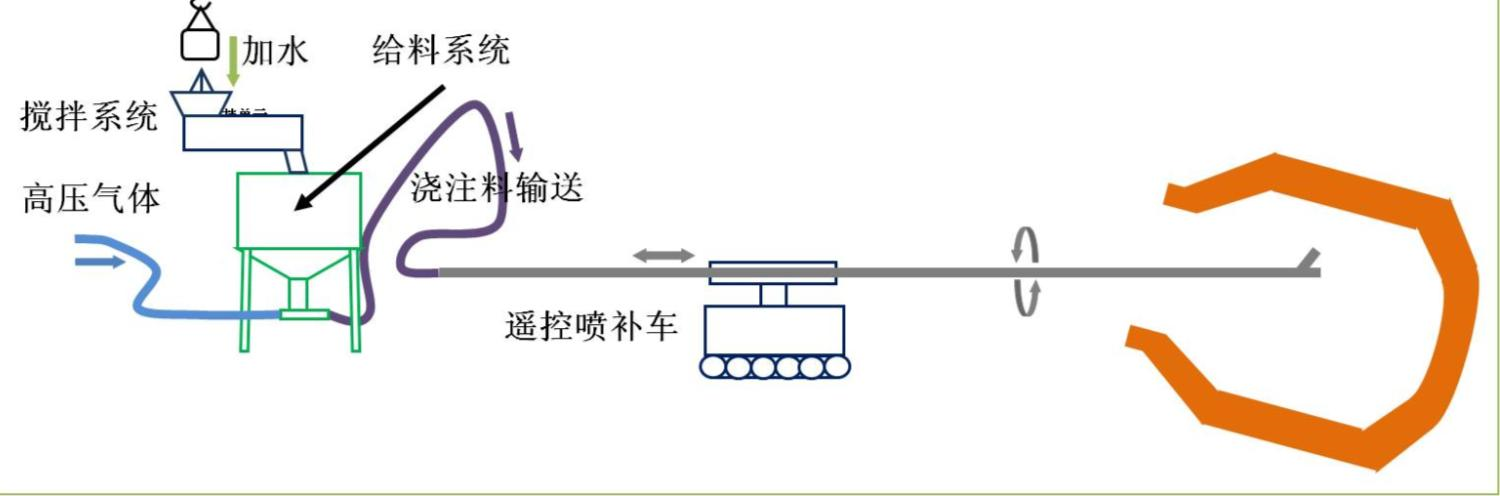
Some enterprises have designed a set of technology and matching equipment in the process of converter shotcrete, and have carried many trials. The shotcrete system of the converter is operated to repaire by the remote control gunning vehicle, and can remotely control the telescopic movement, rotation, tilt, and left and right swing of the gun. This technology has the following characteristics: can realize the long-distance transportation of pre mixing self-flowing material; add high-pressure air in the tail of gun, the self-flowing material is sprayed onto the furnace wall by a telescopic gun with a water cooling system to form a dense refractory patching layer, and the gun extends out to 14 meters. The shotcrete process is different from gunning, and the self-flowing pouring material ejected by the shotcrete process is firmly bonded with the base material without rebounding or flowing. The results show that the technology can improve the working environment, reduce the labor intensity, improve the quality of gunning, prolong the service life of materials and reduce the frequency of gunning.
The performance of the shotcrete material is better than that of dry (half-dry) gunning material, and it can be predicted that the corrosion resistance and erosion resistance will be greatly improved when the technology is put into the converter for maintenance and repair.
At the same time, the technology can not only meet the needs of shotcrete on the side wall of the converter, but also be used for directional shotcrete repair of the gas permeable brick. Because we found the use of pad materials in the converter maintenance work, the service life of side wall is generally better than the bottom. There are two reasons, one is the bottom-blown and steel of the bottom erosion is more serious, but it is not the main reason, the more important factor is that the process of repairing the bottom, in order to prevent the blockage of gas permeable brick, it has been in the air supply condition, patching materials has been mixing by airflow, the bottom of the materials in the curing process of sintering, some break up by air, impact the service life.
In short, environmentally friendly water-based converter pads self-flowing material is a environmental friendly and high efficiency converter pads material, it basically solves the problems of the traditional pads material, greatly improves the production efficiency of the converter and achieves the effect of increasing production and increasing efficiency. Shotcrete repair technology will achieve the conversion that high performance of Magesia material in converter maintenance from gunning to shotcrete. The remote control of shotcrete operation is realized, the labor intensity in front of the furnace is reduced, and the service life of the converter is improved.
Zhang Ronghui concluded that, under the new situation, only rely on technological innovation, can be maintain the survival and development of enterprises. To provide more quality services to users, refractories enterprises need to make greater efforts, to provide users the new materials and the new technology with more environmentally friendly, more relaxed, and more effectively. Through innovation, we may solve the actual problems that existing or new generation in production. Many steel mills are in bad conditions, refractory enterprises have to pay more R&D work in equipment, materials and technology innovation, to adapt to the needs of new development, and make the new contributions to the new development of steel industry and even metallurgical industry.
Asphalt Combined Magnesia Pads Material Repair Converter Site Video
The 260 ton converter of a steel mill uses asphalt combined with magnesia pads material to repair the pads of converter, and the smoke in the site is billowing! But this is the current universal repair operation on Chinese steel converter!
Environmental Friendly Type Water-Based Magnesium Pads Material Repair Converter Site Video
Allied Rongda environmental friendly type water-based magnesium pads material used in 260 tons converter of a plant to repair the pads, without any smoke and dust at the site, sintering time is half of the black material, the service life is two ~ three times more than black material!
Allied Rongda Environmental Friendly Type water-based Pads Patching Material Is a Full Replacement For the Traditional Pads Patching Material!